- #1
DIYEngine235
- 13
- 4
- TL;DR Summary
- Can I convert a power steering pump into a hydraulic motor to provide power to a 4 speed transaxle? Hydraulic power is provided by another power steering pump driven by a 10hp motor.
I'm toying with the idea of building a UTV/ATV using parts from an old John Deere 210 lawn tractor. The main design problem I have is I need to reconfigure the motor relative to the transaxle. The transaxle is a 4 speed Peerless 2300 with reverse. Because of the shift arm location, I have to mount the transaxle under or near the seat. To reposition the motor, I'm exploring the idea of using a pair of power steering pumps, which are basically vane pumps, to create hydrostatic drive to replace the variable size pulley (variator) drive system.
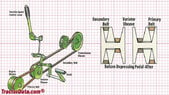
The idea is, I use one PSP (power steering pump) as the pump and convert the other to use as a hydraulic motor to drive the transaxle. Is this idea even possible. If so, what kind of power loss/efficiency would I be looking at? If this sounds feasible, I plan on building a drive calculator to figure out the optimal pulleys to use. I don't have anything more specific than that for the design right now. I just want to know if this is feasible.
The pump is driven by a 10 hp Kohler K241 motor with an operating range of 1700-3500 rpm with max (rated) torque of 16.5 @ 2400 rpm.
Peerless 2300 Gear Ratios
Gear - Ratio
1 - 160:1
2 - 50 :1
3 - 30 :1
4 - 20 :1
R - 40 :1
As for why I'm doing this whole project? Why not?!
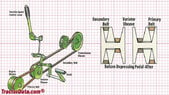
The idea is, I use one PSP (power steering pump) as the pump and convert the other to use as a hydraulic motor to drive the transaxle. Is this idea even possible. If so, what kind of power loss/efficiency would I be looking at? If this sounds feasible, I plan on building a drive calculator to figure out the optimal pulleys to use. I don't have anything more specific than that for the design right now. I just want to know if this is feasible.
The pump is driven by a 10 hp Kohler K241 motor with an operating range of 1700-3500 rpm with max (rated) torque of 16.5 @ 2400 rpm.
Peerless 2300 Gear Ratios
Gear - Ratio
1 - 160:1
2 - 50 :1
3 - 30 :1
4 - 20 :1
R - 40 :1
As for why I'm doing this whole project? Why not?!